
Textiles composites : fabrication de pièces de grande dimension à géométrie complexe
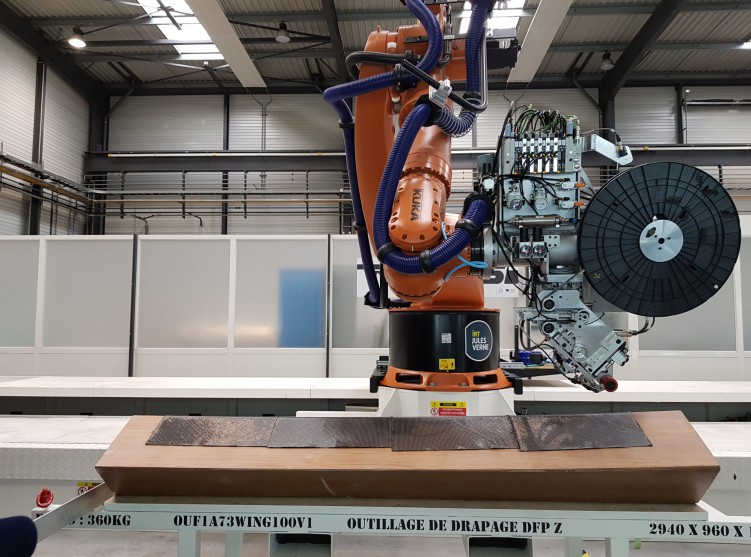
L'IRT Jules Verne inaugurait le 13 février 2020 la plateforme MADRAS, ligne de fabrication de pièces de grande dimension à géométrie complexe en textiles composites pour l'aéronautique. Cette ligne de 18 mètres de long, point central du projet de R&D WING piloté par l'IRT et porté par les partenaires industriels du projet, Airbus, utilisateur final, Fives et Loiretech fabricants de machines, est installée au Technocampus de Nantes. MADRAS propose une innovation de procédés permettant d'augmenter les cadences de fabrication par 5 ou 6, de générer une réduction importante des déchets et de l'empreinte de fabrication de ces pièces sur l'environnement, ainsi que des coûts. Des applications multi-filières sont visées par la suite dans l'automobile, le naval ou l'éolien.
Le projet de R&D WING a démarré en 2017. D’un coût total de 5,6 millions d'euros, ce projet a nécessité des investissements machine de 4 millions d'euros auxquels la région Loire Atlantique et le FEDER ont contribué pour moitié. Le coût de la ligne MADRAS s’élève 1,2 million d'euros. Trois îlots robotisés sont dédiés respectivement au drapage (dépose à plat de tissus multiaxiaux), au préformage rapide et au placement de fibre. Ces étapes, aujourd'hui dissociées, devront être optimisées pour aboutir à une ligne entièrement automatisée.
Deux technologies de drapage de fibres sèches différentes sont utilisées. Une couche de NCF est déposée à plat par machine Fives, en autant de bandes que nécessaire, ce qui limite les chutes. Une couche de DFP par placement de fibres permet de fixer les plis. Ces matériaux sont déjà utilisés par Airbus et fabriqués par ses fournisseurs actuels, Hexcel ou Solvay par exemple. La couture peut faire jusqu'à 4 mètres sans ondulation. Le placement de fibres ne présente pas de limite d’orientation et permet d’obtenir des formes complexes. Le préformage se fait par infrarouge à une cadence élevée grâce à la technologie Loiretech.
L'imprégnation en résine époxy a ensuite lieu au Technocentre. Elle ne fait pas l’objet de recherche particulière mais permet de finaliser le process pour vérifier le résultat final.
Les enjeux pour l’aéronautique Aujourd'hui, Airbus construit en moyenne 10 A350 par mois, capacité qu’elle souhaite porter à plus de 60. D’autre part, la gestion des déchets est devenue un enjeu environnemental majeur. Pour une résistance mécanique donnée, l’utilisation de textiles composites allège fortement la structure des avions. Ils ne sont pas soumis à la corrosion ce qui permet également de réduire les besoins de maintenance des appareils. Ainsi le nombre de cycles a crû de 50% (passage de 40 à 60 cycles). Ils sont utilisés dans le caisson central, la pièce qui subit le plus de tensions mécaniques, mais peuvent être utilisés dans les ailes. Les textiles composites représentent 25% de la structure d'un A380, et 50% dans un A350. Cette proportion pourrait atteindre 75 % dans les prochaines générations.
Résultats attendus et résultats obtenus : Le projet ambitionne de tripler les cadences, pour passer à un taux de dépose de 50 à 150 kg /h soit une vitesse de 200 à 300 mm/s. A l'heure actuelle, il est de 75 kg/h. Le gain en termes de pertes de matière lors de la fabrication est encore plus important. De 100 % de chute, elles passeront de 5 à 10 %, ce qui représente des millions d’euros d’économies. Prochaine étape, la numérisation permettra de simuler le processus complet dès la CAO.
Contact : Anne-Laure Milhe